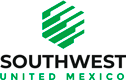
About
Southwest United Galnik SA de CV was legally formed in 2009 as a joint venture between Southwest United Industries, Inc. and Galnik, SA de CV to bring Nadcap accredited aerospace metal processing to Querétaro and Central Mexico. Galnik was established in 1988 and enjoyed sustained growth and is a recognized leader in the Bajio de Mexico area as a certified supplier of processing services for the automotive, electronic, and commercial industries.
Now known as Southwest United de Mexico SA de CV (SWU Mexico), the site constitutes a significant capital investment and provides other aerospace manufacturers the critical processing infrastructure necessary to expand the Querétaro and Mexican manufacturing industry.
Southwest United Industries was acquired by Precision Castparts Corp. in December, 2012.
Our Facilities
PCC Aerostructures Mexico SA de CV operates from a 25,000 sq ft facility in a conveniently located modern building in Querétaro. We relied on our vast experience when configuring the building and equipment making us a world class provider of metal processing services.
- Anodizing (Sulfuric Acid Anodize, Chromic Acid Anodize, Chem Film)
- Non-destructive testing (Primary: Fluorescent Penetrant Inspection (FPI))
- Painting
- Cleaning and Passivation
- Shot Peen Saturation
Services
We are your low-cost solution for surface enhancing and Nadcap-approved finishing in Central Mexico.
Anodizing
Sulfuric Acid Anodize
The sulfuric acid process is by far the most widely used process. It produces films of greater thickness (0.1 to 1.0 mil) and is particularly suited for applications where hardness and some resistance to abrasion is required. However, where parts are subjected to considerable stress, such as aircraft parts, the possible presence of the corrosive acid residue is undesirable. The overall thickness of the coating formed is 67 percent penetration in the substrate and 33 precent growth over the original dimension of the part.
The porous nature of sulfuric acid films prior to sealing is used to particular advantage in the production of colored surface finishes on aluminum and its alloys. The porous aluminum oxide absorbs dyes well, and subsequent sealing helps to prevent color loss in service. Although dyed anodized films are reasonably color-fast, they have a tendancy to bleach under prolonged direct sunlight.
Chromic Acid Anodize
Chromic acid coatings are frequently preferred if there is a possibility of solution entrapment in joints, recesses, and weldments because the chromic acid leaves no corrosive residue. The chromic acid is inhibitive to aluminum and, thus, is especially good for coating aluminum castings.
Chromic acid-produced films are dense, very thin (0.02 to 0.05 mil), light grey in color, and have excellent corrosion resistance. The overall thickness of the coating formed is 50 percent penetration in the substrate and 50 precent growth over the original dimension of the part. Chromic acid films are typically harder than sulfuric acid films of the same thickness.
Chem Film
Chem Film or Chromate Conversion is a chemical treatment process for aluminum used to provide corrosion protection and surface preparation for paint and adhesives. It is an economical alternative to anodizing when abrasion resistance is not required.
All chromate conversion coatings use chromic acid in the form of its soluble salts. During the process, a thin, gel-like film is produced on the aluminum surface. Chromate is an excellent treatment method for paint or adhesives since it greatly enhances the product's ability to form a bond with the aluminum. It is frequently used on electrical and electronic equipment because it provides increased corrosion resistance while remaining electrically conductive. It is also often used on military weapons systems such as tanks, tubing, and component structures where paint finishes are required for the interior surfaces but not the exterior surfaces.
The oxide films produced by this process vary in color from clear to iridescent yellow or brown depending on the aluminum alloy being treated, surface conditions, and the type of chromate.
Non-Destructive Testing (NDT)
Non-destructive testing (NDT) includes inspection methods which are usually used to search for the presence of defects in components. The types of defects detectable include cracks, porosity, voids, burns, and inclusions. NDT is used by our customers to ensure product integrity and reliability, prevent failure and accidents, ensure customer satisfaction, and maintain a uniform quality level.
The primary method used by PCC Aerostructures Mexico SA de CV is fluorescent penetrant inspection.
Fluorescent Penetrant Inspection (FPI)
FPI is most commonly used in the inspection of critical machined parts such as aerospace parts. Florescent penetrant inspection consists of applying a fluorescent dye penetrant to the parts to be inspected. The coating has the property to penetrate any emerging crack and after applying an exposure to ultraviolet light the defects or suspect areas will appear as fluorescent light to the trained inspectors’ eyes.
At Southwest the parts are run through a semi-automatic preparation process. The parts are washed and then dried by a drying oven, then immersed in a bath of dye, the dye is then given time to "dwell" so that emerging cracks of corrosion or defective manufacture will contain the penetrating dye which will then show as fluorescent light once exposed to an ultraviolet light source. The parts are examined by one of several level II or level III certified NDT technicians. Southwest’s technicians have many years of experience in examining aviation parts and are able to perform the examination in a thorough and efficient manner.
Painting
Southwest United de Mexico SA de CV offers complete painting and other metal finishing services to offer our customers full finishing capability. Painting or organic finishing is often used to provide improved corrosion resistance.
Painted finishes can be specified for a number of purposes. The decision to plate or paint for a specific application will often depend on the following considerations:
- Cost – Generally, on a per-unit, surface-area basis, organic coatings will tend to cost less than plated deposits.
- Appearance – The broad range of colors and textures of painted surfaces often make it the finish of choice over plating.
- Corrosion resistance – In many cases, a properly selected paint coating applied over the pretreatment will perform better in outdoor exposures than a plated one
Plating, thermal spray and painting complement each other in providing the best choices of finishes.
Southwest United de Mexico SA de CV is familiar with the best coating systems for improving corrosion resistance on steel, reducing oxidation on aluminum, and other benefits from painting. Contact us to learn how painting can be part of your metal finishing solution.
Miscellaneous
Southwest United de Mexico SA de CV offers metal finishes including cleaning and passivation.
Process | Sub-Processes | Customer | Specs |
---|---|---|---|
Anodizing | Boric Acid - Sulfuric Acid Anodizing Class 1 | Boeing | BAC 5632 |
Anodizing | Boric Acid - Sulfuric Acid Anodizing Class 5 | Boeing | BAC 5632 |
Anodizing | Chromic Acid Anodizing | Bombardier | BAPS 160-010 |
Anodizing | Chromic Acid Anodizing - Class 1 and 3 | Boeing | |
Anodizing | Chromic Acid Anodizing - Class 5 | Boeing | BAC 5019 |
Anodizing | Chromic Acid Anodizing of Alum. - Type I | Boeing | MIL-A-8625 |
Anodizing | Sulfuric Acid Anodize Type II | Boeing | MIL-A-8625 |
Anodizing | Sulfuric Acid Anodizing | Boeing | BAC 5022 |
Anodizing | Sulphuric Acid Anodizing | Bombardier | BAPS 160-032 |
Miscellaneous | Aqueous Degreasing | Bombardier | BAPS 180-040 |
Miscellaneous | Boeing approved QMS | Boeing | Quality System |
Miscellaneous | Captive Laboratory | Bombardier | CAPTIVE LABORATORY |
Miscellaneous | Electrical Bonding of Aircraft | Bombardier | BAPS 145-002 |
Miscellaneous | Evaluation of Paints | Bombardier | BAERD-GEN-018-5E |
Miscellaneous | Process Solution Control | Boeing | Chem. Testing |
Non-Destructive Testing | Corrosion Testing | Bombardier | BAERD-GEN-018-5A |
Non-Destructive Testing | Fluorescent Penetrant Inspection | Bombardier | BAPS 176-002 |
Non-Destructive Testing | Liquid Penetrant Inspection | Boeing | BSS 7039 |
Non-Destructive Testing | Penetrant Inspection | Boeing | BAC 5423 |
Non-Destructive Testing | Salt Spray Testing | Boeing | ASTM-B-11 |
Non-Destructive Testing | Wet Chemistry - Treatment of Solutions | Bombardier | BAERD-GEN-018-1B |
Painting & Coatings | Application of Fluid Resistant (Fr) Enamels | Bombardier | BAPS 138-044 |
Painting & Coatings | Application of Fluid Resistant Primer | Bombardier | BAPS 138-043 |
Painting & Coatings | Application of Polyurethane Enamel (F24 & F37) | Bombardier | PPS 34.03 |
Painting & Coatings | Chemical Conversion Coatings for Aluminum | Boeing | BAC 5719 |
Painting & Coatings | Chemical Conversion Coatings on Aluminum Alloys | Boeing | MIL-DTL-5541 |
Painting & Coatings | Chemical Conversion Treatment For Aluminum Alloys | Bombardier | BAPS 160-020 |
Painting & Coatings | Epoxy Prime | Bombardier | PPS 34.08 |
Pretreatment | Acid Cleaning & Deoxidizing Aluminum Alloys | Bombardier | BAPS 180-032 |
Pretreatment | Alkaline Cleaning | Bombardier | BAPS 180-001 |
Pretreatment | Alkaline Etching of Aluminum Alloys | Bombardier | BAPS 180-030 |
Pretreatment | Cleaning and Stripping of Painted Surfaces | Bombardier | PPS 31.07 |
Pretreatment | Cleaning Processes of Aluminum | Bombardier | PPS 31.02 |
Pretreatment | Passivation of Corrosion Resistant Steel | Bombardier | BAPS 180-015 |
Shot Peening | Shot Peening | Boeing | AMS 2430 |
Shot Peening | Shot Peening | Boeing | BAC 5730 |
Can't find your spec? Please contact us.
Supplier Quality Documents
Title | Notes |
---|---|
Supplier Quality System Questionnaire | AQS1001 - Rev. B |
Supplier Quality Requirements Manual | SQR-10000 - Rev. E |
Matriz de QA's | SWGI-012 - Rev. 0 |
Supplier Quality Requirements | SQR - Rev. B |
Address:
Ave. De la Luz No. 24 Int. 16
Querétaro, QRO 76120
Phone: 011-52-422-209-5184